Over the years I have found that one of the most commonly misunderstood methods of jewelry making is the lost wax casting process. I am frequently asked exactly how casting works. One popular misconception is that the mold is made in wax. Naturally questions soon follow regarding the ability of this material to withstand heat from molten metal. Yes, you would be left with quite a mess if you were to pour 1640-degree sterling silver into a mold constructed of wax! That is not how the process works. In many cases I need to emphasize more than once that the model is the item created in wax and that is molded.
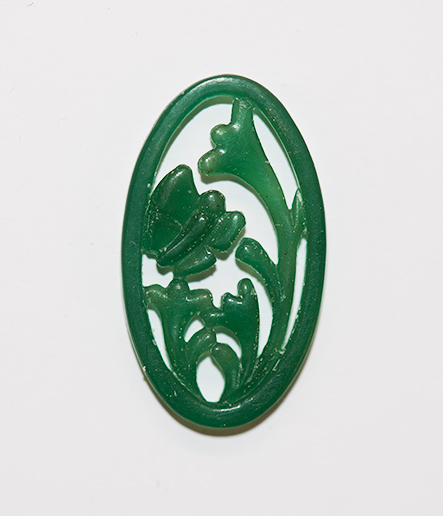
The first step in the process is to create a model. The model is an exact replica of what will become the end product. There are a number of carving waxes on the market to choose from. None resemble that of a candle in any capacity but are closer in consistency to a soft piece of plastic. Carving wax is plastic based and color coded to reveal its specific texture and hardness.
As an artist, of course I hand carve all of my models. Once the model is complete and as close to perfect as humanly possibly a mold can be produced in rubber. The rubber mold will be injected with a different variety of wax that varies dramatically from those designed for carving. Injection wax is somewhat sticky with much greater pliability, a necessary quality to allow it to be pulled from the mold without cracking or breaking.
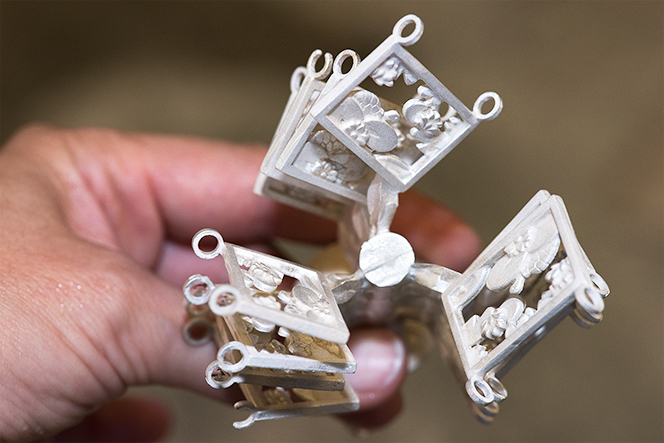
Once a number of production pieces have been compiled they are assembled into the shape of a little tree known as a sprue tree. This figure is built upon a rubber base with a rounded bump in the center. Once complete, a metal flask is placed around the outer rim and investment is poured around the construct. Investment is essentially fireproof plaster. It must be mixed and vacuumed to remove any air bubbles. The slurry will be vacuumed twice, once directly after mixing and once after it has been added to the flask. Investment dries fast! So this step must be preformed in an efficient manor. I can still remember the trying levels of stress that resulted from a poor quality vacuum table at the School of the Museum of Fine Arts. Though most of their equipment was good quality, the vacuum table was frequently problematic. However, every step of this complex operation is important and will determine the quality of the finished product.
Once the investment has fully set the rubber base can be removed and the flask is placed inside a burnout oven. Remarkably the temperature in the burnout oven is so hot that the wax actually evaporates out of the top. Finally, after all of these steps a mold for metal has been produced.
Two methods of casting are commonly used in the jewelry industry. I have used a centrifuge in the past but currently we cast on a vacuum table. A centrifuge spins the molten metal into the flask. If all goes well the flask fills and beautiful castings result. If all goes wrong the flask can blow out leaving bits of investment and scattered shims of metal throughout the inside of the machine.
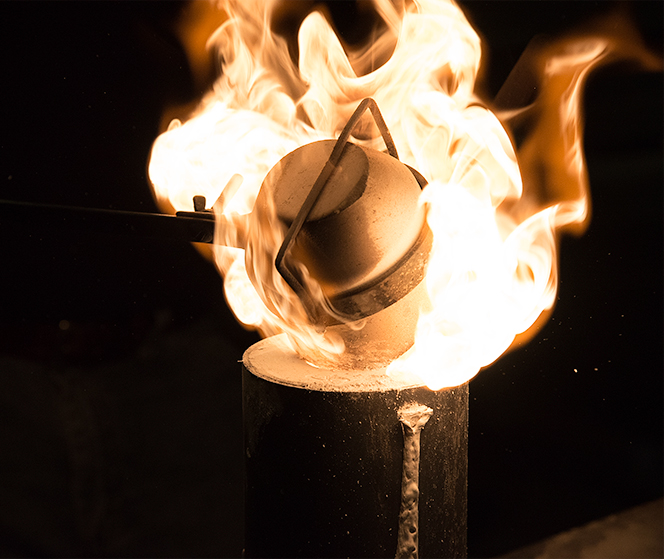
Vacuum casting is quite different and involves placing the flask atop a vacuum table with enough suction to hold the flask firmly in place and also facilitate in pulling the metal into the mold. A major advantage to this technique is the vacuum will also suck out any porosity in the metal, unless it is severe. If metal is overheated porosity can develop. In extreme cases it will not only ruin the casting, but also cause problems down the road when this scrap is later melted. Unlike casting in a centrifuge, vacuum casting involves pouring the metal into the flask by hand. A perfect pour involves accurate timing, heating, and of course aim!
Once cast, the flask must cool for 20 minutes or so before quenching. Repeatedly dipping the flask in a large bucket of water will dissolve the investment leaving a perfect replica of the sprue tree originally built in wax!
Now, the long process of polishing begins….
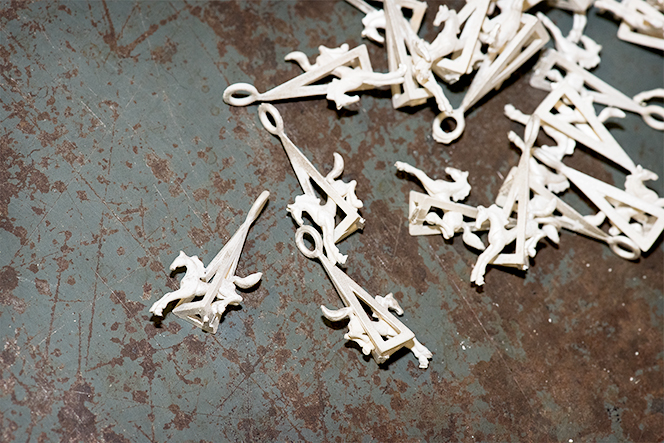